How to Design Pre-Terminated Fiber Cables
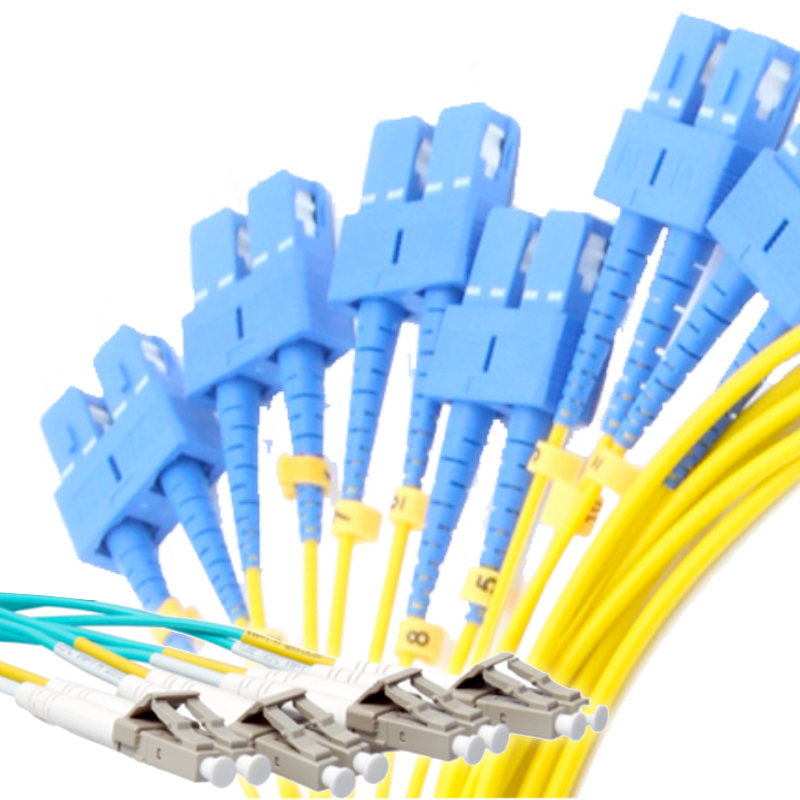
Custom pre-terminated fiber optic cables, or cables that are cut to length and terminated offsite, are a popular option for installations because factory-terminated cables:
- Save time in the field -- simply pull them and plug them into the electronics;
- Are certified for performance within a tight loss parameter;
- Feature stronger and more durable connectors than field-terminated mechanical connectors; and surprisingly
- Are often less expensive than bulk cable and connectors.
That's right, pre-terminated cables can actually save you money because the style of connectors (spliced and/or epoxied) are significantly less expensive than field-installed mechanical connectors. Plus, no onsite termination labor is required.
So what's needed to design and order a pre-terminated fiber optic cable? It starts with a good understanding of optical technology and your installation.
Factor 1: Length
Not surprisingly, proper design and construction of a factory-terminated fiber cable starts with understanding the length of the cable run. This is important to ensure the cable is long enough and to ensure the proper type of fiber is specified.
Multimode fiber typically has a maximum length of 1000 - 2000 feet depending on the signal bandwidth, whereas single mode fiber supports theoretically unlimited bandwidth and distance. You can compare the two types in an online article.
Best practice for determining cable run length is to take as accurate a measurement as possible and add at least 20 feet. Modern fiber supports bend ratings under 0.5 inches, allowing it to be coiled into a service loop inside or below enclosures.
Factor 2: Strand Count
Strand count, or how many glass strands are physically present in the cable, is also important. Most electronics require a duplex connection (duplex referring to two fiber strands). Many pre-terminated cables are built with some redundancy and expansion capability, and it's common to see 6 strand and 12 strand pre-terminated cables.
Factor 3: Connector Type
Obviously a factory-terminated cable requires an understanding of what type of connectors must be terminated onto the cable. You can compare the different fiber connectors in an online article.
It helps to understand the type / make / model of device that will be connected to the fiber optic cable -- the port on the device will feature an LC, SC, FC or possibly an ST connection. If multiple devices will be connected to a multi-strand cable (see factor 2 above), factory pre-terminated cables can even be built with multiple different connectors.
If you are not sure what type of connector is required because the device isn't specified yet, we typically recommend LC connectors because they have become the most common connection type for networking, AV and even security electronics. Plus, LC connectors can be converted in the field using a fiber adapter.
Factor 4: Jacket Material
The cable's jacket material is also critical, and jacket specification is entirely based on the installation environment. Different materials and cable constructions are explored in an online article.
For example, local building codes might require riser or plenum jackets and outdoor installations might require a water-rated jacket.
Factor 5: Armor
The final consideration for properly specifying and ordering a factory-terminated cable is armoring. In fact, armored cables are often factory terminated because it can be difficult to cut and handle metal armor in the field.
Cables buried directly in soil, also known as direct burial cables, require armor for protection from cutting, rodents and abrasive environmental cycles (such as erosion and freeze/thaw cycles). Indoor cables exposed to regular handling or abrasion also benefit from armoring.
Pre-Terminated Cable Concerns
Integrators considering factory-terminated cables often have concerns over the durability, workability and future serviceability of the cables. Below is a list of common questions and answers.
Question / Concern | Answer |
How strong are pre-terminated cables? | Fiber optic cables, including pre-terminated cables, are surprisingly strong. Most feature a pull-rating between 25 - 100 lbs. |
What about when pulling through conduit? Will pre-terminated cables survive? | Pre-terminated cables are typically built with pull-mesh covering the end of the cable and connectors. This provides protection and strength. |
Question / Concern | Answer |
What size conduit will pre-terminated cables fit through? | We typically recommend conduit diameters of 3/4" or larger for most pre-terminated cables. Higher strand count cables will often feature staggered connectors to reduce the pulling footprint. |
What happens if my cable is damaged during the pull? | Pre-terminated cables feature the same bulk fiber that you'd handle and terminate in the field. They can easily be re-terminated if damaged or a shorter cable length is desired. |
How long does it take to receive a pre-terminated cable? | Manufacturing typically takes 3 - 5 days for most cables. Plan on a little extra time depending on transit distance. |
Comments